
Potash Plant Concrete Replacement, Jordan
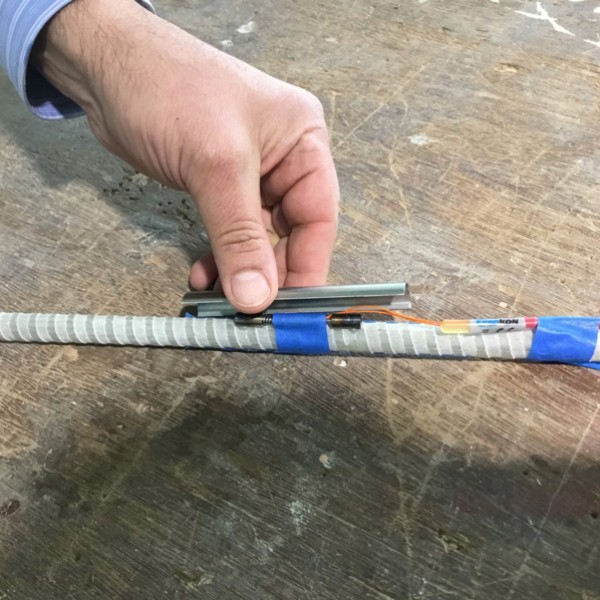
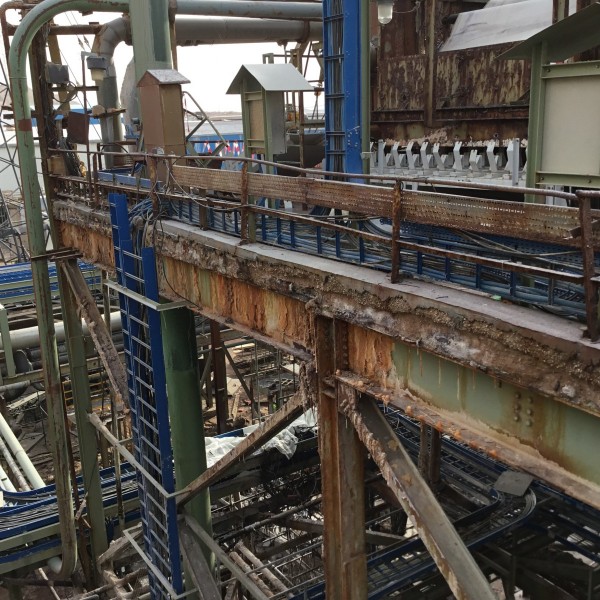
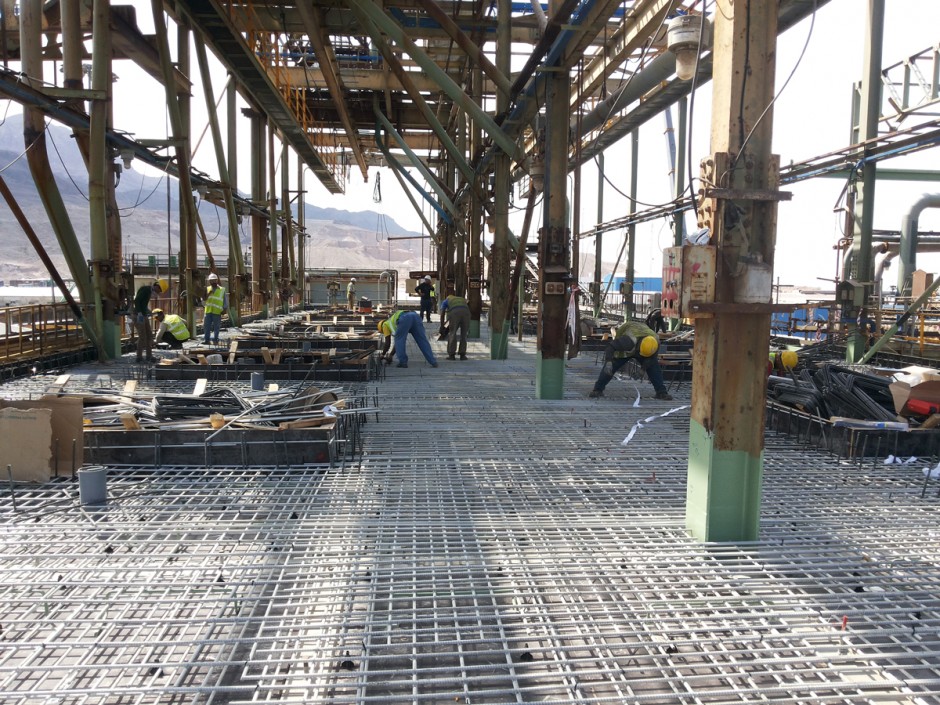
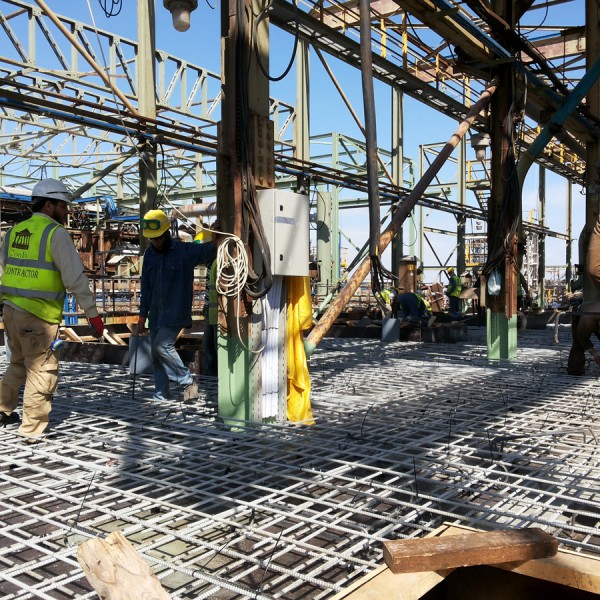
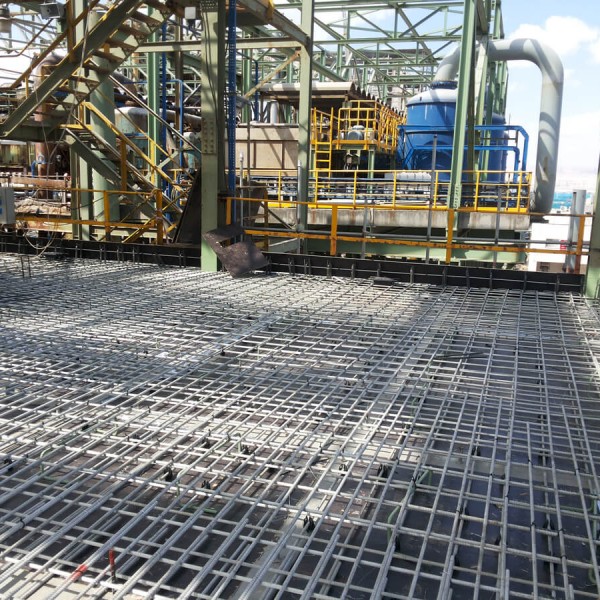
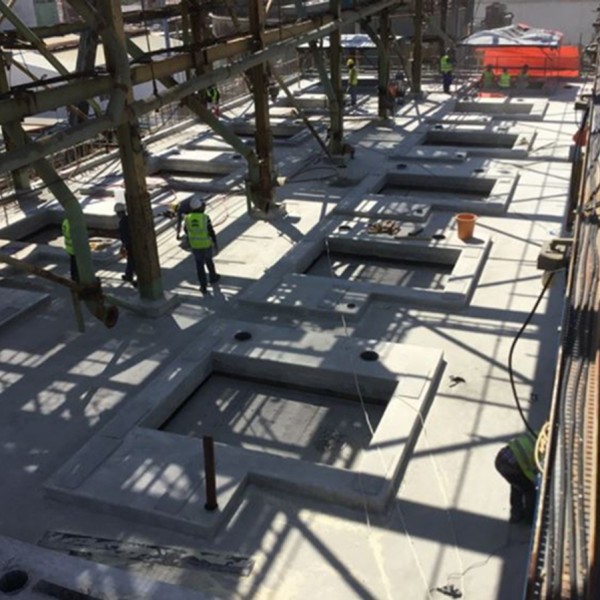
Project Overview
The Carnallite Structure at the Ghor El Safi potash plant in Jordan is a five-story, open steel-framed facility built in the 1980s.
It houses an elevated concrete slab and steel framework supporting centrifuge machines, key to the hot leach production line. The plant produces around 500,000 tons of potash annually in a highly corrosive environment.
Potash production involves extracting saline water from the Dead Sea and concentrating it in solar and carnallite ponds before processing it in hot leach and cold crystallization plants.
Exposure to harsh chemicals, including chlorides and salts, accelerates concrete and steel deterioration. Over time, the hot leach product (HLP) severely degraded the concrete slab and steel framework, causing premature corrosion.
To maintain safe and efficient operations, engineers designed a replacement slab resistant to chemical damage and vibrations from the centrifuge machines.
Glass fiber-reinforced polymer (GFRP) rebar was chosen as the primary reinforcement for the project, with Mateenbar60™ selected for its superior performance in aggressive environments and ability to withstand the plant’s unique stresses.
Project Results
The use of Mateenbar60™ fiberglass rebar provided key advantages for the potash plant, including:
- High resistance to chemical exposure, including harsh chlorides and salts
- Long-term durability, reducing the risk of premature concrete failure
- Resistance to sustained and cyclic loading caused by the vibration of centrifuge machines
- Extended service life of at least 60 years, even under extreme environmental conditions
- Lower maintenance costs and reduced production downtime
To validate the effectiveness of the new concrete slab, engineers embedded dynamic sensors within the structure to measure vibration performance post-installation.
The results confirmed that the Mateenbar60™ reinforced slab effectively managed the plant’s demands, ensuring a durable and reliable foundation for years to come.
By integrating advanced materials like Mateenbar60™, the Ghor El Safi potash plant successfully extended the lifespan of its critical infrastructure while reducing long-term maintenance requirements.
This project serves as a model for using innovative solutions in highly corrosive industrial environments, demonstrating the importance of material selection in optimizing structural resilience.
See our project post over the Perth Seawater Desalination Plant in Western Australia for another example of how Mateenbar60™ reigns as the best choice for reinforcing large structures in marine environments.
Building the Future with Mateenbar®
For over 30 years globally, Mateenbar® has been a leader in strength, purpose, and sustainable innovation—proudly made in the USA and fully BABA-compliant. When infrastructure projects demand proven durability, superior performance, and long-term resilience, Mateenbar60™ is the smart choice. Contact our team today to learn how GFRP rebar can optimize your next project, reduce lifecycle costs, and deliver lasting results. Discover why Mateenbar® reinforces what matters most—building the future of infrastructure, one project at a time.